COMMON PCB DESIGN ERRORS
COPPER PATTERN
We look at common Printed Circuit Board errors in Cad files. To make manufacturing PCB's efficient and time-saving, we recommend the below solutions to avoid these errors. Copper Pattern errors are the first topic in our common design error series.
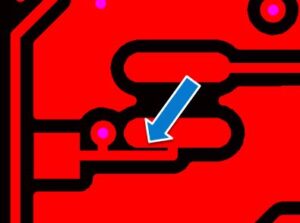
Problem Description:
Same net spacing difficulties are commonly seen in that the setup in the CAD systems has different (lower) values for the same net spacing than the spacing between different nets. This can cause problems in the same nets with too low isolations in the same nets which result in sliver problems and/or result in solder mask openings exposing nearby copper.
Solution:
To avoid such problems. It can advised to use the same settings for “same net spacing” as for “different net spacing”.
Problem Description:
With boards with plated copper and if as standard all holes are drilled together for best hole position tolerances. In some designs, copper features are too near to non-plated holes or copper features cover non-plated holes. For copper features too near to non-plated holes, it would after tolerances result in damaged copper features as damaged traces and pads or may result in copper plating residues in non-plated hole wall. Also, depending on production factory processes it may be impossible to produce such a design as it would cause cracked dry film in PCB production. And such cracked dry film may peel off causing film scrap on board and faulty boards. Or if copper features totally cover non-plated holes then it would cause non-plated holes to change to plated holes.
Solution A:
In PCB production it is preferred that all holes are drilled together in the same drilling process for best hole position tolerances, so to drill all holes together and to avoid the above problems and to remain non-plated holes as non-plated, it is recommended to design copper features at least 250µm distance from non-plated hole edges (applies to 35µm final copper thickness). For thicker copper, other values are applied (for example for 70µm finished copper than 300µm distance is recommended from copper features to non-plated hole edges).
Solution B:
If copper features are too near to non-plated hole edges or if copper features totally cover non-plated holes, then there is a less suitable solution as a second drilling process is possible for such non-plated holes. However, the second drilling process disadvantage is that it may result in exposed copper and eventual burrs at non-plated hole edges, as after tolerances the second drilled holes may cut into the too near copper features. Also second drilled non-plated holes may result worse than standard hole position tolerances which is another reason if possible to avoid this solution. The exposed copper at non-plated hole edges may also cause a shortage after the customer assembly process. (For example, if the same non-plated hole cause exposed copper on several copper layers with different nets). So if this solution B is used then the customer also must be sure that there is no risk for an eventual shortage problem.
Problem Description:
One net copper feature too near to another net plated hole edges – may cause a shortage between different nets.
Solution:
It is recommended to keep a distance of at least 300µm between one net copper features to another net plated component hole edges (at least 250µm from standard via hole edges) to avoid the risks of shortage. Of course, more distance is even better (applies to 35µm final copper thickness). For thicker copper, other values are applied. (Example, if 70µm finished copper then at least 350µm distance is recommended from one net copper feature edge to another net plated component hole edge). (at least 300µm from standard via hole edges). Of course, more distance is even better.
Problem Description:
Such design may cause uneven copper plating thicknesses. And on layers with copper plating where the “bow & twist” then cannot meet the recommended standard.
Solution:
To avoid such problems, copper should be as evenly spread as possible on the same layer. And also as symmetrical/balanced as possible between different copper layers.
Problem Description:
Too small “Flooding spacing” towards most parts of patterns, makes the production more difficult than it needs to be. This can then affect the price.
Solution:
In most cases, there is no reason to have too small “Flooding spacing". So a good value is to use a value of 150-250µm between the flooding and board features.
Problem description:
Copper clearances are too small towards board outline. (and/or towards non-plated slots). And may cause exposed copper and burrs along the board outline (or along with non-plated slots). Eventual different net exposed copper at board edges or non-plated slots may also cause shortage after the customer assembly process. (For example if exposed copper on several copper layers with different nets). Also in many cases, the designers need to take into consideration that the assembly process often needs some sort of array with v-cut (scoring) or routing with break tabs. It is therefore good to plan the design for this and make room for break tabs and/or v-cut.
Solution:
To avoid burrs and exposed copper at outlines (and at non-plated slots). A good rule for design is to keep copper features at least 0,25mm from the routed outlines and from non-plated slot edges. (Applies to 35µm final copper thickness). For thicker copper, other (more) values are applied. If routed outlines, then also consider having suitable copper-free areas along with the outlines for break tabs (and for break tab holes). At such places copper at least 0,7mm from outlines and the copper-free areas approximately with 5mm lengths. For v-cut keep at least a 0,45mm distance between copper and v-cut outlines (applies to 35µm final copper thickness). For thicker copper, other (more) values are applied. Also please note that for v-cut boards thicker than 1.6mm the clearance from copper to outline needs to be further increased.
Problem description:
Too small texts/numbers in copper - may result in unclear texts on finished boards. Problems in PCB production as too small texts/numbers often have parts with very small isolations (small slivers in copper) which may peel off in production resulting in shorts, opens and solderability problems.
Solution A:
As the first choice, it is recommended to design all texts/numbers only in silkscreen layer (s). The recommended text line width is 0.13mm or more and with a text height of at least 0.8mm. The silkscreen should be designed to avoid solder mask open areas and to avoid holes. Only use necessary numbers (text) in copper (for example layer numbers) and then of course with correct sizes (see other solution.
Solution B:
To avoid such text problems and if the other solution (silkscreen) is not possible, then it is recommended to use a copper line width of 0,2mm or more with a text/number height of 2mm or more (bigger is better). Also important to keep enough clearance between copper text lines.